The pages within this guide.
Static Mixing Guide
In this guide, we will discuss the process and how we go about selecting the correct static mixer for your application.
"Do you need an agitated tank or could you use an inline pipe static mixer?"
Fluid mechanics such as plug flow, Reynolds number, and pressure drop play a key role.
The mixer length and the number of mixing elements based on the mixing device are based on experience and laboratory studies. We will shed some light here as well.
The most common applications are blending of chemicals.
Dispersions, whether gas-liquid or liquid-liquid, are critical in some processes.
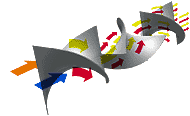
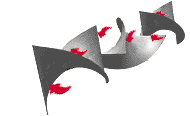
Characteristics of a Static Mixer
Simple Construction
- Consistent Cross-Sections
- No Space for Fluid Buildup.
Metrics:
- No Pressure Loss
- Easy to Upgrade
- Easy to Clean
Inline Construction
- Shut Out From Outside Air
Metrics:
- Safe Working Environment
- Clean Operation
- Space Saving
Radial Mixing
- Nearly Ideal Piston Flow
Metrics:
- Safer Control Systems
- Continuous & Uniformed Operation
- Easy Expansion
No Actuator
- Maintenance Free
Metrics:
- Nearly No Wearing Parts
- Simple Installation
- No Power Supply Necessary
Metrics:
- Energy Efficient
- Explosion Safe Area Installation Possible
Mixing of Liquid-Liquid | Mixing of Liquid-Gas | Mixing of Gas-Gas | For Testing |
---|---|---|---|
Mutual Solubility of Two Liquids (Good) | Drainage pH Adjustment | Adjusting of Atmosphere Gas | Visual Observation of the Fluid Mixture |
Mutual Solubility of Two Liquids (Bad) | Aeration | Gaseous Fuel Adjusting | Test by the Small Lots |
Dilution, Neutralization, Compounding | Carbonation | By-product Gas Recycling | |
Dispersion, Extraction, Emulsification | Deoxidation of Organic Liquid | Denitrification of Flue Gas | |
Addition/pH Adjustment | Temperature Homogenization of High Temperature Gas | ||
Alkali Cleaning | |||
Super Critical Liquid Extraction |
Chemical Fiber Spinning Process Use | Extruder Use | Injection Molder Use |
---|---|---|
Improvement of the viscosity and the temperature irregularity in the distribution tube. | Improvement of the viscosity and the temperature irregularity occurring in the extruder. | Improvement of the viscosity and the temperature irregularity occurring in the injection molder. |
Dissimilar Polymer Blend | ||
Improvement of the viscosity and the temperature irregularity in the spinning nozzle. | ||
Mixing of Additive |
Direct Heating (Injecting steam directly into liquid to condensate) | Direct Cooling (Injecting cold water directly in steam to vaporize) | Indirect Heating (Heating of heat transfer liquid) | Indirect Cooling (Cooling of refrigerant liquid) |
---|---|---|---|
Warm Water Production | Temperature decrease and low pressure steam production | Heating of the process liquid | Cooling of the process liquid |
Heating of Chemicals | Heating of the chemical raw materials (polymer) | Cooling of the raw chemical materials (polymer) | |
Heating of Slurry | Viscosity adjustment by flash heating the coating liquid of de-monomers | Cooling of raw food materials | |
Heating/Sterilization of highly viscous liquid. | Viscosity adjustment of coating liquids |
Chlorination reaction | Absorption of low pressure liquid |
Production of Ammonia Water | Absorption collection of reaction gas |
Production of Liquid Bleach of Pulp | Production of Ozone Water |